Manufacturing Process Optimization: Steps & Examples
Manufacturing Process Optimization Success In 7 Steps
Efficient manufacturing is critical to meeting the rising demands around the globe. But, while U.S. manufacturing contributed $2.3 trillion to the GDP in 2020 alone, actual manufacturing industry productivity is down. The right manufacturing process optimization can make all the difference, but finding time to effectively tackle this is easier said than done.
If you’re wanting to get more out of your manufacturing efforts, you’re not alone. Fifty-six percent of customers want new products faster than before. Fortunately, you can ace manufacturing process optimization through a series of best practices. And, with the implementation of digital twin technology, you can even go beyond your facility’s current capabilities to gain an even bigger competitive advantage.
What is manufacturing process optimization?
Manufacturing process optimization is the practice of reducing downtime and increasing output within manufacturing by streamlining operations and worksite flow. Additional goals of manufacturing process optimization often include reducing errors and waste, lowering energy use, minimizing risk, and more.
To achieve manufacturing process optimization, leaders typically look at multiple core areas:
Worksites
Processes
Equipment
Change management
The above categories may look different depending on your type of facilities and the products you’re manufacturing, but the goal is always the same: to improve output and minimize waste.
Why is manufacturing process optimization important?
While manufacturing process optimization is a nuanced practice, the rewards are worthwhile. There are a number of benefits that come with manufacturing process optimization, beyond the obvious.
Reduced error rate
Because manufacturing process improvement involves rethinking proper equipment use and ideal process and worksite setups, you can naturally find a reduced error rate and less need for rework.
If you’re practicing manufacturing process optimization, you likely have the right materials at the right stations, the right equipment being used properly and maintained, and processes that efficiently utilize employee time. This combination can keep employees on task while lowering the risk of someone grabbing the wrong material or a piece of equipment malfunctioning.
Elevated product quality
Along with a reduced error rate comes more consistent quality and a boost in customer satisfaction. But, not only is consistent quality on the table, you can strive for elevated product quality as you continue refining processes.
Time is one of your largest enemies in manufacturing, as it limits what you’re capable of accomplishing within a day. When you’re optimizing entire processes, you’re getting back time that can be spent on further optimizations. Ongoing improvements lead to the ability to deliver at an elevated capacity, be it to meet more demand or to even higher quality products that your brand can be proud of.
Reduced downtime for manufacturing equipment
Unplanned maintenance and equipment downtime not only grinds production to a halt, it also comes with a large financial cost — 11% of the yearly turnover for Fortune Global 500 companies.
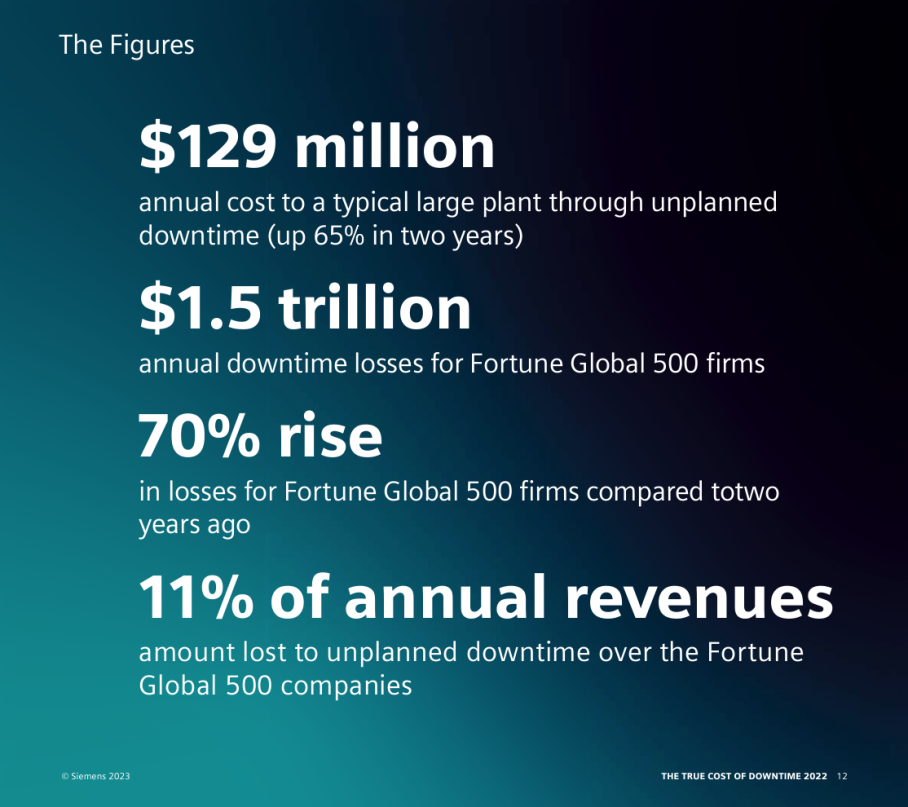
By optimizing equipment use and maintenance schedules, along with ensuring staff are trained on the latest equipment protocols, you can reduce the likelihood of an avoidable equipment failure. This not only helps you avoid the hefty price tag of equipment downtime, but also allows you to more accurately forecast production as there will be fewer disruptions.
Decreased manufacturing and production costs
Time is money, especially in manufacturing. By streamlining existing processes to reduce time and material waste, and reducing the likelihood of equipment downtime, you’re able to ultimately decrease manufacturing and production costs. Much like improving quality, the right manufacturing process optimization methods allow you to continue making strides toward further profitability, too.
Increased productivity
Naturally, as you streamline workstations and current processes, you will increase productivity. Fewer incidences of equipment downtime and maintenance will also help with productivity, as your team won’t be on hold while something is fixed.
An added perk, you could also see a bump in employee morale, on account of production optimization and fewer avoidable headaches.
Streamlined supply chain management
Supply chain management is especially difficult when you can’t accurately forecast your materials use, and when you’re losing materials to inefficient processes and mistakes.
By streamlining worksites and processes and ultimately reducing materials waste, you’re able to more accurately forecast material needs in the coming quarters. This allows you to order in advance and avoid falling victim to shortages.
This also works on your end as a supplier, as more consistent production allows you to make accurate delivery contracts with clients purchasing your products in bulk.
7 steps for optimizing manufacturing processes
Manufacturing process optimization takes time and careful preparation. But, with the right approach and team of stakeholders, you can soon be optimizing manufacturing processes and set your organization up for long-term success.
1. Identify improvement areas
The first thing you need to do is figure out where your biggest opportunities for improvement are. You can approach this a couple of ways.
Focus on highest-dollar problems
Prioritize quick wins
Take a combined approach to maximize gains and minimize resources required
As you look for opportunities and consider your approach, look at any available data to identify potential candidates for process improvement. This is also a good time to loop in your employees and ask them about frustrations with certain workflows or equipment, as there could be issues data doesn’t show.
2. Collect real-time data
Manufacturing process optimization is a data-driven activity. Data is critical to making the most informed decisions and figuring out where you should focus optimization efforts. Real-time data also allows you to see if your efforts are working or not.
Newer machines will likely have the appropriate sensors to capture production data, but older ones may not. If you have older machines that aren’t collecting data, equip them with the right sensors before beginning any optimization efforts. While newly-equipped machines won’t yield the ideal historical data you want for optimization, they can still deliver a smaller window of insight. And, these machines will at least be equipped to show post-optimization performance.
You also want data on employee performance and movement around the workspaces. Make sure you have some form of tracking to capture foot traffic, whether you’re using RFID tags, sensors, or other tech to do so. This will help you map out current workflows and analyze them for potential optimization, and monitor workflows afterward.
Keep in mind, data from older machines and new machines, along with data from employee movement and workflows, will likely be spread across a number of systems. Again, this is a great time to consider using a platform that consolidates internet of things (IoT) data into one dashboard, like AWS IoT TwinMaker.
3. Analyze bottlenecks
While you’re collecting data, it’s important to look for production line bottlenecks, both those noticeable via data and outside data. If you see clear layout-related issues on the floor, these are ideal bottlenecks to tackle with manufacturing process optimization.
You should also turn toward your training processes here as well. Interview employees about any current knowledge gaps, as well as any onboarding struggles. Because change management is a critical component of manufacturing process optimization, it’s important to address training-related issues as early as possible.
4. Automate repetitive processes
You’ve worked hard to assemble the team you have, so it only makes sense that you deliver a valuable workplace experience and elevate them. Automating repetitive tasks can free them up and allow them to focus on more challenging work.
As you map out your optimization project, flag repetitive processes and look into process automation solutions for these tasks. Ideally, you want artificial intelligence (AI) and machine learning (ML) solutions that are capable of not only automating the work, but also doing the work faster over time.
Some prime examples of manufacturing-related tasks you can automate include:
Inventory management
Sales processing
Order processing
Data collection and logging
Report generation
You can also use AI and ML-powered solutions to help with data analysis and decision-making. Some of these advanced tools can even help you with production and financial forecasting, as well as predicting gains from optimizations.
5. Utilize IoT-enriched digital twins
It’s possible you have stakeholders in other locations. You may also be planning on optimizing manufacturing for numerous locations. In the past, these scenarios resulted in expensive travel and delays in decision-making.
Using digital twins for manufacturing, you can invite your stakeholders to virtual tours and walk them through a space. You can then enrich these digital twins with IoT data from your equipment and applications using AWS IoT TwinMaker. With this information, you and your team can virtually walk a space and see operational and maintenance history, video feeds, real-time process data, and more.
This level of data, available in a digital twin, enables informed decision-making no matter where you are. The end result is improved decision-making, the ability to streamline renovations and optimizations across numerous worksites, and reduced travel costs.
For example, RemSense created the first version of its Virtual Plant for training, but the product can also be used for business process optimizations like inspections, hazard analysis, and inventory management. The digital twins render imagery in 4K resolution even when users zoom in. RemSense exports that imagery and data into its asset recognition software that can read and catalog the text strings and numbers on cable and machinery ID tags, providing clients and their contractors and service providers with the granular level of detail they need to manage complex processes remotely.
RemSense identified 540,000 text strings with numbers or words, then automatically compared them to the client’s asset list for validation, then culled irrelevant text captured on signs, notebooks, nametags, and phones. Every piece of equipment verified as a true asset with existing client data was then geospatially tagged. From there, RemSense brought in maintenance data, asset data, operational information, and live IoT data. And it used Matterport as the spatial visual fabric to tie everything together into its first Virtual Plant.
Even if you’re only optimizing one location with all your stakeholders under one roof, IoT-enriched digital twins can help you make the most-informed decision possible, and make it easier to pitch your vision to stakeholders.
6. Monitor performance
By this point you should have thorough monitoring set up across your manufacturing processes. Continue to monitor key performance metrics (KPIs) as you roll out your optimization techniques. Expect a slight slump at first, as people train and get used to the new processes, workflows, layouts, and equipment.
Set milestones for your optimization, from quarterly to annual etc. Take note of your manufacturing organization’s performance as you approach these milestones. If you’re falling well below your goal, go back through the steps and look for underlying issues. If you’re grossly overshooting your business goals, it could be time to aim even higher.
7. Lower risk with transparency
Both before you embark on your optimization journey and after, it’s important to practice transparency. Transparent communication and reporting allows your stakeholders to offer the best input, keeps them aware of the situation and any challenges, and builds trust.
Transparency is also a core part of change management. Keep your team, even non-stakeholders, in the loop with changes as they’re finalized. Then, practice that same transparency as the optimization goes live and update your team members on how performance is going, and so on.
By practicing transparency, you’re setting yourself and your team up for collaborative success. Even if your first manufacturing process optimization efforts aren’t a huge success, your transparent communications can keep your team behind you, and set you up for future successes — no matter what.
Matterport enables transparent communication by making information more accessible across teams and geographies. For example, Danone uses Matterport’s tour features and clickable Tags that include embedded text and video to tell stories, aid in training, and create 3D documentation.
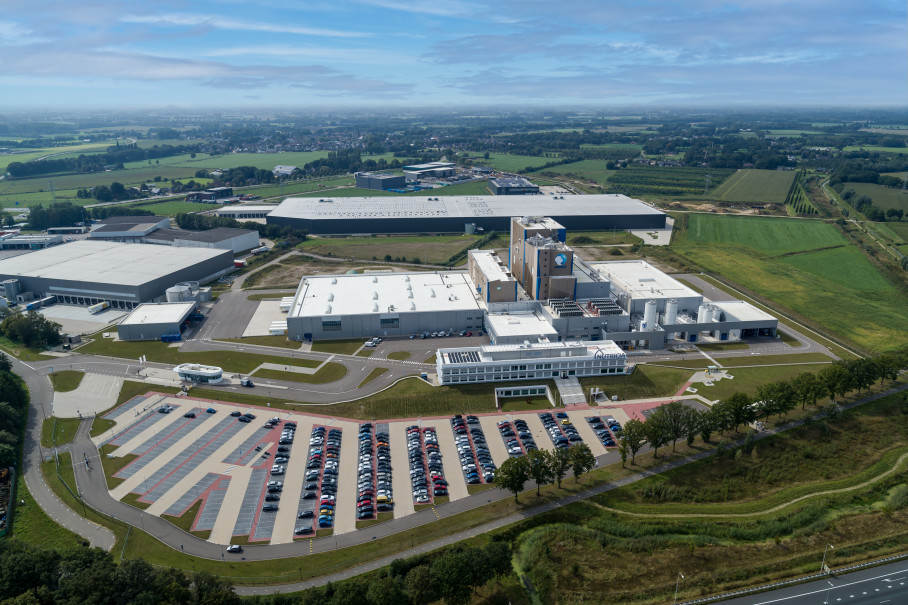
With the collaboration tools and data layers, information can be filtered for different groups across their globally distributed organization. The safety teams, quality teams, maintenance teams, and project teams all require their own sets of information. And they can add comments in Tags, making it easy for information sharing to become more streamlined.
How digital twins help optimize manufacturing processes
Here is a real example of how Siemens used digital twins to collaborate with their clients to optimize manufacturing facilities and enable remote monitoring. In late 2022, Siemens successfully created high-resolution digital twins of one of its manufacturing plants in Asia, encompassing 4,000 m². These digital replicas have proven instrumental in enabling virtual discussions with customers about Siemens' manufacturing capabilities.
The Matterport digital twins facilitate in-depth reviews of production setups without operational disruptions, offering a comprehensive view of spaces and equipment. Siemens is exploring the use of virtual reality (VR) headsets for tours to reduce unauthorized photography and cut down on travel costs. Read more about how technology can improve processes in our article on digital transformation in manufacturing.
We are always on the lookout for novel solutions that can enhance the way we do business. In Matterport, we saw an opportunity to provide immersive, intuitive experiences that were far superior to photography and an inexpensive alternative to other scanning solutions.” — Alexandre Piedade, Incubation Manager, Siemens.
Read the full case study here.
See more on our Facilities Management page.